Essential Maintenance Metrics Every Planner Needs to Know
Get Free Guide
Is a breakdown maintenance plan even possible?
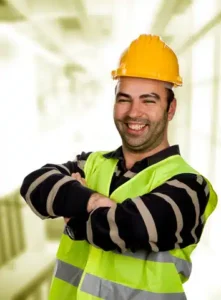
How can one plan for breakdown maintenance? It is by nature very unpredictable!
However, there are some things that you can do. This will make your maintenance team better in handling unplanned equipment breakdowns and other maintenance emergencies.
Breakdown maintenance planning tips
1. Prioritize your preventive maintenance tasks
Set three task priorities. “High” – must complete on time. “Medium” – must complete but can be rescheduled. “Low” – good to do, can be skipped once in a while.
Use your maintenance software put together a maintenance schedule for machinery. This should include all these types of tasks during your work day. Say something unexpected and urgent comes up. You can reschedule or skip preventive maintenance work of “Low” and “Medium” priority. This will make time to attend to corrective maintenance.
2. Analyze your historical work orders
See if there are times when equipment tends to break down. For example you may see a seasonal change when the weather turns hot or cold. Or more frequent breakdowns during busy seasons when equipment is heavily used.
Once you confirm such trends there are a few things you can do to prepare. For instance, make sure that your maintenance staffing levels are adequate during those periods. Encourage people to take vacations during less busy periods. Schedule training during quieter periods. Hire temporary staff and so on.
3. Prioritize equipment based on whether delays in fixing them are acceptable
For example if one of several similar machines fail it may not be so much of an emergency. Other machines may be able to handle the lost production. Or you may be able to “borrow” a replacement from the vendor. This will give you some flexibility in deciding when to fix equipment break downs.
4. Use historical data to identify equipment that breaks down frequently
Find the most common causes of failure. Plan preventive maintenance to reduce such breakdowns. You may also want to replace such equipment if more reliable options are available. See “Analyzing Machine/ Equipment Breakdown Reports From CMMS Software” for more on using these reports.
5. Use historical data to find the most common equipment failures
Ensure that they are not happening due to user or operator errors. For instance they may be overloading a machine. Or they may ignore equipment warnings and so on. Make sure that technicians are trained to fix such breakdowns soon. This will ensure a fast turn-around and increase customer and end user satisfaction.
6. Improve spare parts availability
This can be hard to do since breakdowns are not predictable. But not having spares to fix an equipment breakdown will cause delays. Keeping a large supply of (possibly costly) spare parts on hand adds to maintenance expenses.
Again historical data can be useful. It can give you an idea of spare parts and supplies you need to have on hand to handle most types of common breakdowns. You may also be able to find vendors who can get you spares and supplies quickly. The article “6 Ways CMMS/ Maintenance Software Can Improve Vendor Management” has some useful information.
7. Review manufacturer recommendations regularly
Make sure that you are following recommended practices when doing maintenance. Some missed maintenance steps can be the reason for certain equipment failures.
Do you have problems collecting this information?
These tips require you to collect and analyze a lot of maintenance data. This works best with a CMMS/ maintenance software program.
Do not have CMMS software? Or are the reports from your existing program inadequate? You can get a fully functional 30-day trial of FastMaint CMMS software.
Use the import feature to import your equipment from comma delimited files. Try out reports mentioned to see how it can be used for better breakdown maintenance planning.
Free FastMaint CMMS TrialUseful resources
The US Environmental Protection Agency (EPA) in a section for Lean Manufacturing and Environment has an article “Lean Thinking and Methods” which has several tips on reducing & managing breakdowns.
Essential Maintenance Metrics Every Planner Needs to Know
Get Free Guide