Essential Maintenance Metrics Every Planner Needs to Know
Get Free Guide
Deferred maintenance – two words that can send shivers down the spines of facility managers and property owners alike. From spiraling repair costs to safety hazards and diminished property value, the repercussions of postponing maintenance can be severe.
So, what exactly does deferred maintenance entail? Why is it such a pressing concern? And, most importantly, how can one tackle an ever-growing maintenance backlog?
In this article, we’ll provide tangible examples, evaluate the true cost of deferring upkeep, and offer actionable tips to finally start clearing your maintenance backlog.
What is deferred maintenance?
Deferred maintenance is the deliberate delay of planned or unplanned maintenance activities on assets or facilities that should have been addressed immediately. This results in a maintenance backlog that accumulates over time.
While some organizations might see it as a temporary solution to budget constraints or resource shortages, the long-term implications are often far-reaching.
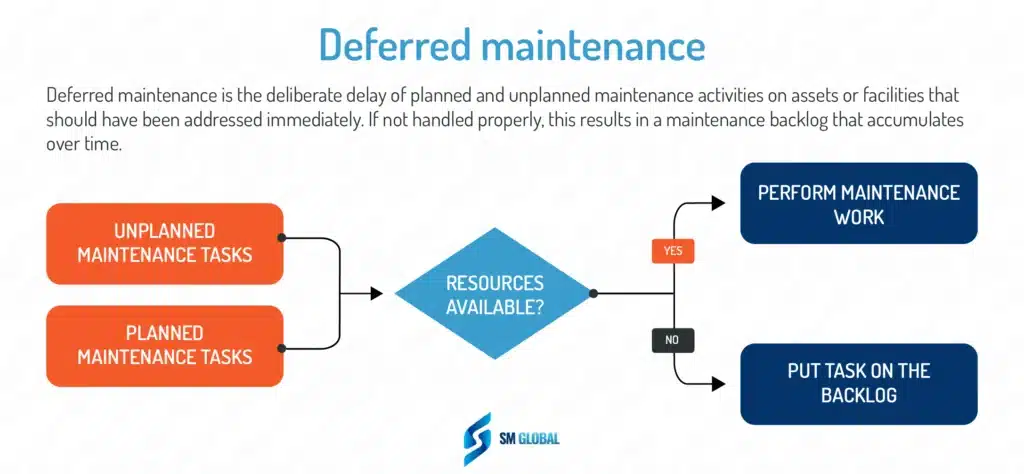
Here are the most common causes of deferred maintenance:
- Budgetary constraints: One of the most common reasons for deferring maintenance is the lack of available funds. When organizations face tight budgets, maintenance often becomes a lower priority, leading to necessary tasks being pushed to a later date.
- Resource shortages: Sometimes, even if the funds are available, there might be a lack of manpower, equipment, parts, or expertise to carry out the required maintenance activities on time.
- Poor planning: Without proper maintenance planning and scheduling and a proactive approach, tasks can easily be overlooked or underestimated, resulting in unexpected delays and backlogs.
- Inadequate asset tracking: In larger organizations with hundreds or thousands of assets, the lack of a robust asset management system can lead to some maintenance requirements falling through the cracks — and having to be put on the backlog once identified.
- Misaligned priorities: Often, reactive tasks or short-term priorities take precedence over planned preventive maintenance, leading to a gradual accumulation of deferred tasks.
A few deferred maintenance examples
A deferred maintenance example from a manufacturing facility
In a large manufacturing plant, a CNC milling machine, vital for precision parts production, begins showing signs of wear. Over time, the calibration starts to drift, leading to slight inaccuracies in the produced parts. The management recognizes the need for maintenance. However, due to a lack of technicians trained specifically for CNC calibration and repair, the necessary maintenance is postponed.
As days turn into weeks, the inaccuracies become more pronounced, leading to a significant number of defective parts and eventually causing unplanned downtime.
A deferred maintenance example from property management
An apartment complex starts experiencing roofing issues in several buildings. Residents report minor leaks, especially during heavy rains. Even though roofs require immediate attention to prevent water damage and mold growth, the property management company, facing financial constraints, decides to postpone the needed roof repairs to the next fiscal year.
This delay results in escalated repair costs as minor leaks turn into significant structural damage in some buildings.
A deferred maintenance example from the hospitality industry
In a boutique hotel nestled in a tourist hotspot, the HVAC system is essential for ensuring guests’ comfort. The hotel management is aware of the annual maintenance schedule for this HVAC system. However, due to poor planning, they schedule a major event at the hotel during the same period the system is due for maintenance. They have to delay the HVAC servicing to avoid inconveniencing event attendees.
The true costs of leaving deferred maintenance unchecked
It’s not hard to see the appeal of deferred maintenance. By postponing certain tasks, organizations can free up resources to address more urgent needs in the short term.
However, if not managed properly, deferred maintenance can cause all kinds of issues down the line:
- Escalated repair costs: Small issues that are easy to fix in their initial stages can escalate into much costlier problems. For instance, a minor crack in a building’s foundation, if ignored, can lead to significant structural damage requiring extensive repairs.
- Operational downtime: Equipment or facilities that aren’t maintained may break down more frequently or unexpectedly, disrupting normal operations. This can lead to lost revenue, especially in sectors like manufacturing where consistent production is critical.
- Decreased asset lifespan: Assets that aren’t regularly maintained will have a shorter operational life.
- Safety risks: One of the most severe consequences of deferred maintenance is the potential safety hazards it can introduce through equipment malfunctions, structural failures, and other risks.
- Reputation damage: In the age of online reviews, a single maintenance oversight can quickly become public knowledge. Businesses, especially those in the hospitality sector, can face significant reputation damage by postponing upkeep.
- Decreased property value: For property managers and real estate investors, deferred maintenance can significantly reduce the value of the property. Potential buyers or tenants will often factor in the cost and hassle of addressing maintenance backlogs when considering a property.
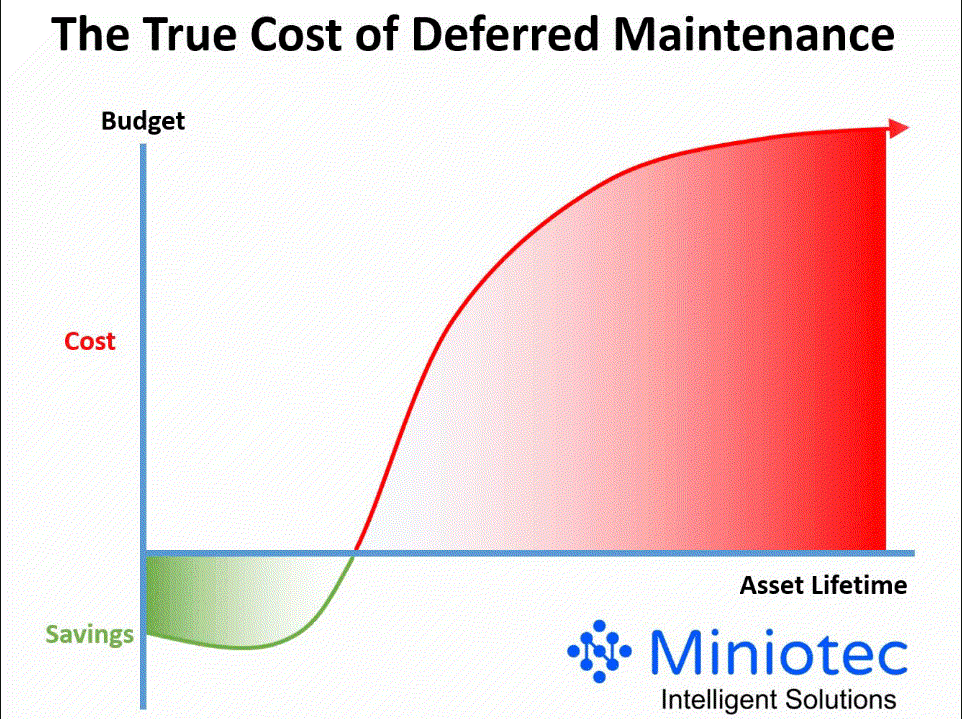
Long story short, deferred maintenance is a helpful tool in the facility manager’s arsenal — as long as it is not abused — as the consequences can be dire.
How to start clearing your maintenance backlog
Years of accumulated tasks, combined with the existing day-to-day workload, can make the challenge appear insurmountable. However, with the right approach and a structured plan, it should be possible to bring the backlog down to manageable levels.
From ensuring the accuracy of your backlog to crafting a robust maintenance plan for the future, these strategies will guide you toward a more sustainable and efficient maintenance regime.
Make sure your backlog is up to date
For maintenance and facility managers, the first step in addressing a maintenance backlog is having a clear picture of its current state. Trying to clear out an outdated backlog can lead to wasted resources and misdirected efforts.
Here’s how to ensure your backlog is (and remains) updated:
- Audit existing records: Review maintenance records, work orders, and service requests. Cross off tasks that have been completed and add any new tasks that may not have been logged.
- Engage with your team: Talk with your technicians. They can provide insights into tasks that might have been overlooked or underestimated in your current records.
- Use digital tools: Consider adopting a CMMS if you haven’t already. Systems like FastMaint can help you prioritize, schedule, and track all of your maintenance tasks.
- Periodically validate with physical checks: While records and systems are valuable, nothing replaces on-the-ground verification. Conduct regular walkthroughs of your facility to identify any visible signs of wear, damage, or other maintenance needs that might not have been reported.
Make a cost-based case to get more resources
While reorganization can help, in many cases, it will be hard to make a significant dent in your maintenance backlog without additional resources. The best way to secure it is to demonstrate the financial implications of deferred maintenance.
Making a compelling cost-based case can convince upper management that they need to invest money to save money.
Start by documenting the immediate costs of deferred maintenance (emergency repairs, lost productivity, non-compliance fines…), forecasting future expenses, and highlighting safety risks.
Then, illustrate the potential ROI — how investing in maintenance now can lead to savings in the long run. If possible, compare your organization’s maintenance spend with industry benchmarks or competitors. This can offer a perspective on whether your organization is under-investing in maintenance.
Leverage CMMS and other records to gather data. Once you have it, present it in a clear and compelling manner. Use charts, graphs, and other visual aids to make your case more persuasive to stakeholders.
Create a deferred maintenance plan
Having a plan specifically designed for deferred maintenance is crucial to systematically address and prevent a growing backlog.
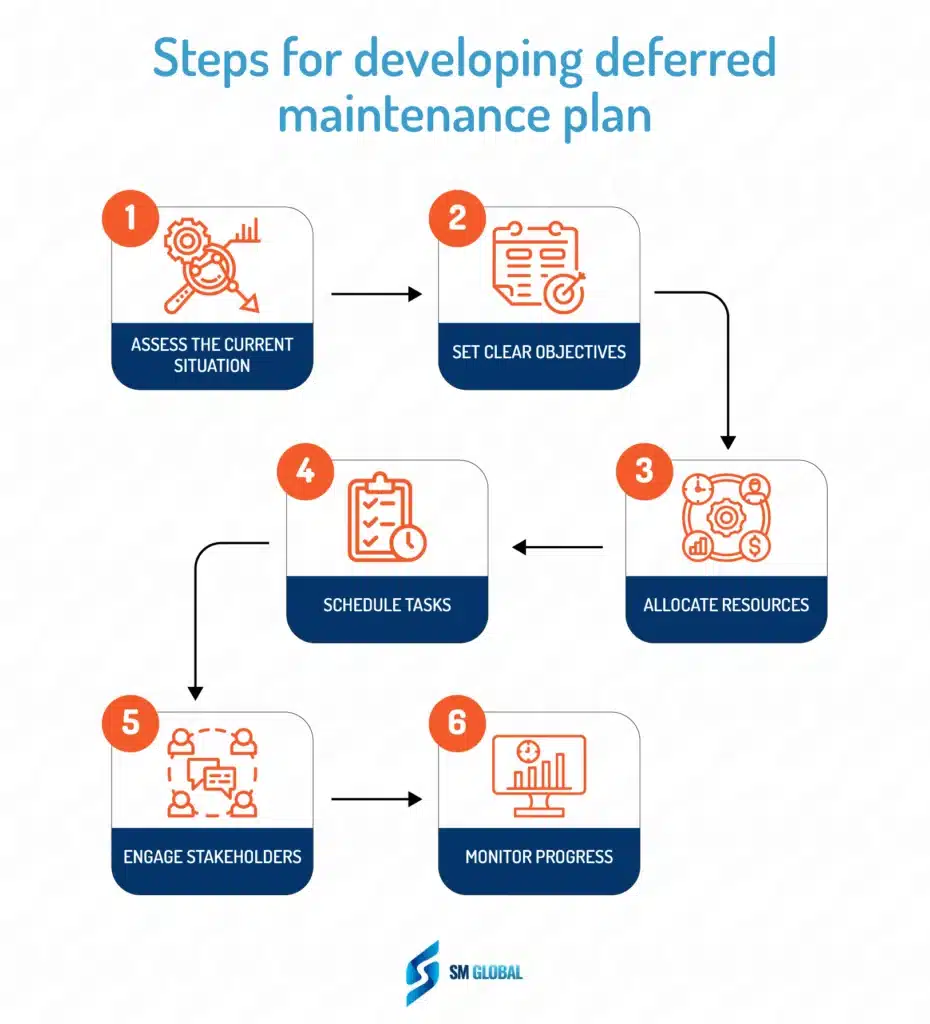
Here’s how to craft an effective deferred maintenance plan:
- Assess the current situation: Start by cataloging all deferred tasks. Include details such as the nature of the task, equipment involved, reasons for deferral, and any associated costs or risks.
- Set clear objectives: Define what success looks like. Is it to completely eliminate the backlog within a year? Or to address all high-priority tasks within six months? Having clear goals will guide your efforts and provide a metric for measuring progress.
- Allocate resources: Determine what resources (personnel, equipment, budget) are available and how they can be best utilized to address the backlog. Consider reallocating or acquiring additional resources if necessary.
- Schedule tasks: Using the prioritization system discussed below, create a detailed schedule. Ensure that urgent tasks are addressed first, but also allocate time for less urgent tasks to prevent them from becoming critical.
- Engage stakeholders: Keep other departments and leadership informed about your plan. Their support can be invaluable, especially when it comes to allocating resources or adjusting operational schedules to accommodate maintenance work.
- Monitor progress: Regularly check the status of your deferred maintenance plan. Are tasks being completed as scheduled? Are there any new challenges or changes that require adjustments to the plan? Adjust accordingly.
As you work through the existing backlog, start thinking about strategies to prevent new ones. This might involve more proactive maintenance, better resource allocation, or adjustments in operational procedures.
Place more focus on proactive maintenance
If you want to reduce your maintenance backlog — and prevent tasks from pilling up again in the future — you need to switch from reactive to proactive maintenance.
You’ll never get to the deferred tasks if 80% of your maintenance team’s time is spent running around and putting out fires.
The best way to start being proactive is to identify important assets that historically caused the most issues and put them on a preventive maintenance schedule. You can use it as a pilot project to instill the new mindset and gradually introduce the whole team to the new workflow.
Implement a clear system for prioritizing maintenance work
Not all work orders are created equal. Efficiently tackling your maintenance backlog requires a systematic approach to prioritizing tasks.
Here’s how you can establish a clear prioritization system:
- Categorize by urgency: Divide tasks into categories such as ‘Critical’, ‘High Priority’, ‘Medium Priority’, and ‘Low Priority’. Critical tasks may include those that pose safety risks or could lead to significant operational downtime.
- Assess the impact on operations: Prioritize tasks based on their impact on overall operations. Equipment that is central to your core operations should be given higher priority over ancillary equipment.
- Consider safety implications: Any maintenance tasks that, if deferred, could jeopardize the safety of staff, customers, or the public should be elevated in priority.
- Evaluate cost implications: Understand which deferred tasks might lead to higher costs if further delayed. Addressing these earlier can result in long-term savings.
- Leverage technology: Utilize Computerized Maintenance Management Systems (CMMS) or other digital tools that can help automate the prioritization process based on set criteria.
- Involve the team: Ensure that your maintenance team is aligned with the prioritization system. Regularly gather their feedback, as they may have insights into nuances or changes on the ground that aren’t immediately apparent.
- Regularly review and update: Just as with the maintenance backlog itself, the system for prioritization should be dynamic. As organizational goals, equipment status, and other factors change, adjust your prioritization criteria accordingly.
Implementing all of these tips should get you on the right track.
Stay on top of deferred maintenance with FastMaint CMMS
Backlogs, if left unchecked, can spiral out of control, leading to operational issues, escalating costs, and potential safety concerns.
With its user-friendly interface, real-time tracking capabilities, and robust analytics, FastMaint CMMS will help you answer all of your deferred maintenance challenges. It will ensure maintenance tasks are seamlessly logged and categorized, preventing any oversight and ensuring each task gets the attention it deserves. You can monitor the progress of tasks, granting managers the flexibility to make on-the-fly adjustments.
While the challenges posed by deferred maintenance are real, they aren’t insurmountable. Start a free trial and get your maintenance back on track with the right plan and strategies, supported by FastMaint CMMS.
Essential Maintenance Metrics Every Planner Needs to Know
Get Free Guide