Essential Maintenance Metrics Every Planner Needs to Know
Get Free Guide
Equipment maintenance Workflow Setup
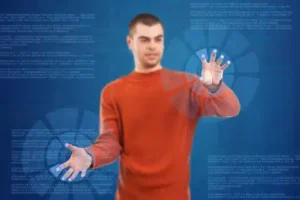
Well organized maintenance programs have a clear equipment maintenance workflow (see the diagram below). For instance a workflow with the following steps:
- External users or customers send in maintenance work requests.
- We schedule this maintenance work as well as preventive maintenance and create work orders.
- Technicians receive these work orders and complete them.
- We generate maintenance reports and so on.
But that’s just part of the story…
What is a workflow? A workflow consists of an orchestrated and repeatable pattern of business activity enabled by the systematic organization of resources into processes that transform materials, provide services, or process information. (source Wikipedia)
Failures in these maintenance workflow processes will cause many issues. We can have problems during each flow shown in the maintenance workflow diagram below. Each flow is shown by an arrow.
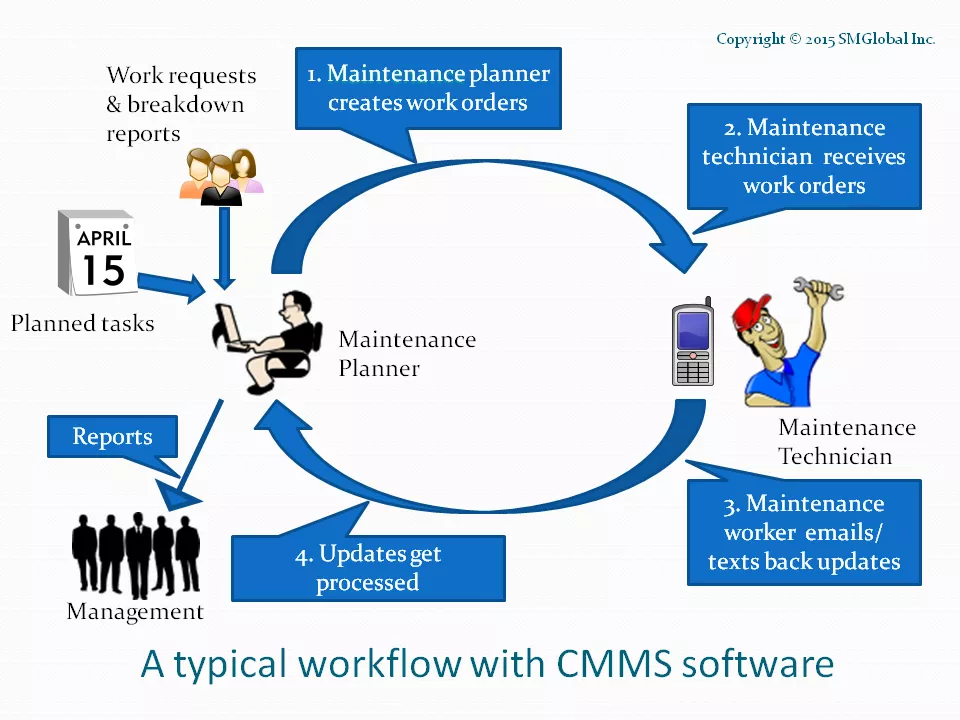
Different Equipment Maintenance Workflow Failures & Impacts
1. Missing work requests or equipment breakdown reports
External users such as customers, equipment operators and so on, can submit requests for maintenance work or report equipment breakdowns. For instance, let’s say several maintenance requests come in each day. We may miss some of these requests in the queue. So the maintenance work never gets done. We may also ignore or miss alarms or problems reported on critical equipment. As a result cascading equipment failures may follow.
Sounds familiar … Have you ever had this happen to you?
This is where maintenance software is very useful. Above all it helps keep track of these requests and reports. In addition, we can use the information provided to create maintenance work orders for maintenance technicians.
2. Preventive maintenance work not being scheduled
Different equipment and facilities will have different planned maintenance needs. For example changing air filters regularly on HVAC units, checking oil levels on specific machines and so on. Hence, missing this preventive maintenance or not scheduling them at the right time can result in equipment breakdowns and other operational issues.
With CMMS software we can schedule planned maintenance and generate the work orders needed. To clarify, see How To Schedule Preventive Maintenance Work Orders for how this done.
3. Work orders not sent out
The right maintenance technicians should receive the maintenance work orders once created. The CMMS program can email these or send them as text messages to the technicians or outside contractors. Alternatively we can print out the work orders and distribute them.
4. Technicians forget to do work or send back completion status
In addition, we can use maintenance software to keep track of pending work orders and receive status updates from technicians. To clarify, these can be received as email or text and used to update and close pending work orders. Most importantly, if they forget to complete a work order or report the status, we can have the CMMS program send out reminders!
5. Poor reporting to management
Most certainly our management team will want regular and easy to understand reports on the maintenance department’s work. However, trying to do this manually will be time consuming & difficult.
Hence, we can use the CMMS software to make standard reports and compare performance with prior periods. See 3 Quick Maintenance Metrics For Maintenance Planners for the types of information that we may need to provide.
In conclusion equipment maintenance workflow failures impose big costs!
We can see that many of these workflow failures can have a big impact on the maintenance program. Dropped or incomplete maintenance can result in cascading breakdowns. As a result the maintenance department will be seen as incompetent!
Not being able to give good and on-time reports to management is also bad. As a result they will make decisions on maintenance budgets based on poor information. Often this will have a bad impact on the maintenance department.
With good maintenance scheduling software (aka CMMS program), maintenance managers and maintenance planners can avoid or reduce such problems.
Select the right Maintenance Management Software
Looking for CMMS software for your maintenance department? With hundreds of programs available making the right choice can be hard!
A tip – most software review sites are not what they seem. Many are advertiser funded, so we are often guided to products that are not be suitable for our needs.
This free “CMMS Software Selection Guide” has a variety of tips for your own evaluation. Use it to find the right product for your needs. Good luck!
Free CMMS Software Selection GuideEssential Maintenance Metrics Every Planner Needs to Know
Get Free Guide