Essential Maintenance Metrics Every Planner Needs to Know
Get Free Guide
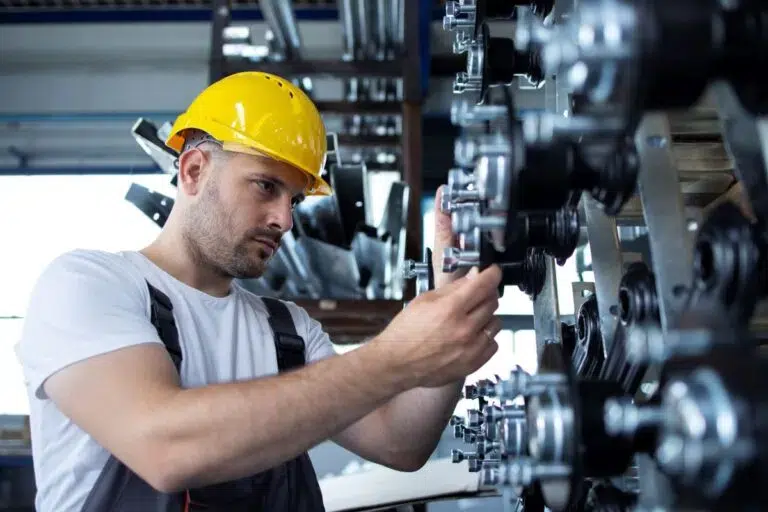
Whether it’s ensuring that a manufacturing production line runs without hitches or a tractor on a farm operates efficiently, machine maintenance makes sure that the used equipment is safe and functional while minimizing the total cost of ownership.
Join us as we explore the best practices for keeping your machinery in top operating condition year-round, without breaking the bank.
What is machine maintenance?
Machine maintenance represents a set of recurring actions that ensure equipment and machinery are operating at optimal efficiency and safety. It involves regular inspections, servicing, repairs, and part replacements to minimize downtime, prevent unexpected breakdowns, and extend the equipment’s lifespan.
Machine maintenance is applied in virtually every industry. That said, it is more recognized in manufacturing, transportation, power generation, construction, and other industries that are heavily reliant on physical assets.
On the operational level, machine maintenance takes different shapes based on which maintenance strategies you are using at your facility.
(If you are familiar with the main types of maintenance strategies and their differences, click here to skip over to the next section.)
Types of machine maintenance strategies you can employ
You’re probably familiar with all of the standard machine maintenance strategies. Each offers unique benefits and is particularly suited to different operational contexts and types of machinery.
Below is a quick head-to-head comparison of the four most commonly used maintenance strategies based on operational differences and implementation costs.
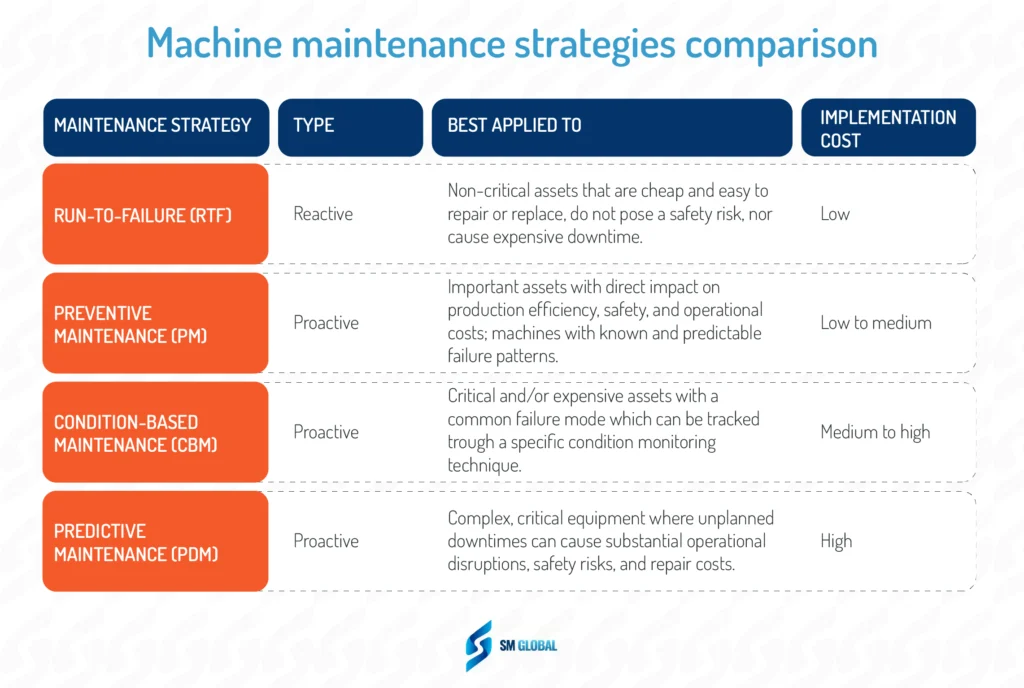
1. Run-to-failure maintenance
Run-to-Failure (RTF) is a reactive maintenance strategy where equipment and machinery are intentionally allowed to operate until they break down. Little to no proactive maintenance is performed on the assets, and actions are only taken once a failure occurs.
Types of assets it is best used for
Non-critical assets that are cheap and easy to repair or replace, do not pose a safety risk, and will not cause expensive downtime. It can also be applied to assets that are at the very end of their useful life.
Examples include office equipment, hand tools, lighting fixtures, an asset you plan to replace the next time it fails, etc.
Typical machine maintenance actions taken to perform RTF:
- Identifying failures
- Diagnosing failures
- Performing corrective actions
- Replacing failed components
Cost to implement
It is a low-cost strategy as expenses are incurred only for repairs or replacements and the associated labor. However, indirect costs such as unplanned downtime and potential impacts on operations and safety can be significant.
RTF example
In a manufacturing facility, cooling fans are used to prevent overheating of machinery. Using a Run-to-Failure maintenance strategy, the fans are allowed to operate until they fail, without any routine checks. Upon failure, a technician diagnoses the issue and replaces the fan.
While this approach may result in some unplanned downtime, the simplicity and low cost of replacing these fans can make RTF a viable maintenance strategy, provided that the failure doesn’t lead to extensive machinery overheating or associated damage.
2. Preventive maintenance
Preventive Maintenance (PM) is a proactive maintenance strategy aimed at reducing the likelihood of machine failure by performing regular maintenance tasks. PM tasks are scheduled based on time or usage cycles, ensuring that machinery and equipment are regularly maintained.
Types of assets it is best used for
Preventive maintenance is well-suited for important assets that have a direct impact on production efficiency, safety, and operational costs. It is typically applied to machines with known and predictable failure patterns, including motors, pumps, and various types of production machinery.
Typical machine maintenance actions taken to perform PM:
- Scheduling regular inspections based on time intervals or equipment usage cycles
- Replacing wear-prone components before they fail
- Cleaning, lubricating, and adjusting machinery parts to optimize performance
- Performing tests and measurements to monitor equipment condition
Cost to implement
Preventive maintenance incurs some upfront costs related to planning, labor, and materials. Though it requires an investment in regular care, it often results in overall cost savings by reducing the frequency and severity of breakdowns, leading to reduced downtime and extended equipment lifespan.
Preventive Maintenance example
A manufacturing facility employs preventive maintenance for its conveyor belt system, crucial for continuous production flow. Maintenance technicians follow a schedule to inspect, clean, and lubricate the system and replace worn-out rollers and belts periodically.
3. Condition-based maintenance
Condition-Based Maintenance (CBM) is a strategy that involves using various types of sensors to monitor the condition of equipment to determine maintenance needs. Maintenance is performed when equipment conditions exceed preset thresholds, indicating potential performance issues or impending failure.
Types of assets it is best used for
CBM is particularly beneficial for complex, expensive, and critical assets where unexpected failures can lead to significant operational disruptions, safety risks, and repair costs.
It’s commonly used in turbines, compressors, high-performance industrial motors, and other assets where a common failure mode can be easily tracked with a specific condition monitoring technique.
Typical machine maintenance actions taken to perform CBM:
- Installing sensors and monitoring equipment to collect real-time data on machinery conditions
- Analyzing data to identify patterns and potential issues
- Performing maintenance tasks when equipment conditions indicate a need, such as unusual vibrations, elevated temperatures, or abnormal noises
- Adjusting operational parameters to optimize performance based on monitored conditions
Cost to implement
The initial cost for CBM can be significant due to the investment in monitoring technologies and analytics tools. However, it often leads to cost savings over time by preventing unexpected breakdowns, reducing maintenance frequency, and extending equipment life.
CBM example
In a manufacturing facility, CBM is employed for a critical CNC machine. Sensors are installed to monitor parameters like temperature, vibration, and pressure in real time. When the system detects elevated vibration levels exceeding the set threshold, maintenance technicians are alerted to inspect and address the issue.
4. Predictive maintenance
Predictive Maintenance (PdM) is an advanced maintenance strategy that uses equipment conditions and other data to build algorithms that can predict when equipment will fail or require maintenance. This approach allows organizations to schedule maintenance tasks just in time to address the issues, minimizing downtime and maintenance costs.
Types of assets it is best used for
PdM is ideal for expensive, critical equipment where unplanned downtimes can have substantial impacts on production and safety. This approach is commonly applied to assets like industrial robots, elevators, and other high-priority assets and production systems where predictive data can significantly inform maintenance schedules.
Typical machine maintenance actions taken to perform PdM:
- Installing/retrofitting condition monitoring sensors and IoT devices on select equipment
- Scheduling maintenance tasks based on predictive analytics insights to address issues before failures occur
- Performing scheduled maintenance actions
Cost to implement
PdM involves a significant initial investment in advanced data analytics, machine learning technologies, and often IoT devices to collect and analyze equipment data. However, it can lead to substantial cost savings by optimizing maintenance schedules, reducing unplanned downtimes, and extending equipment life.
PdM example
An automotive manufacturing plant employs predictive maintenance for its robotic arms, integral for assembly lines. Sensors embedded within the robots send real-time data to a central analytics system. The system employs machine learning algorithms to analyze this data and predict potential mechanical issues or failures. When a potential issue is detected, maintenance is scheduled proactively to address the problem before a failure occurs.
How to keep your machinery in peak operating condition
Selecting the right maintenance strategy for your machinery is just the first step.
Let’s explore comprehensive and actionable steps to optimize the health and performance of your machinery, ensuring that they deliver consistent, reliable, and efficient service year-round.
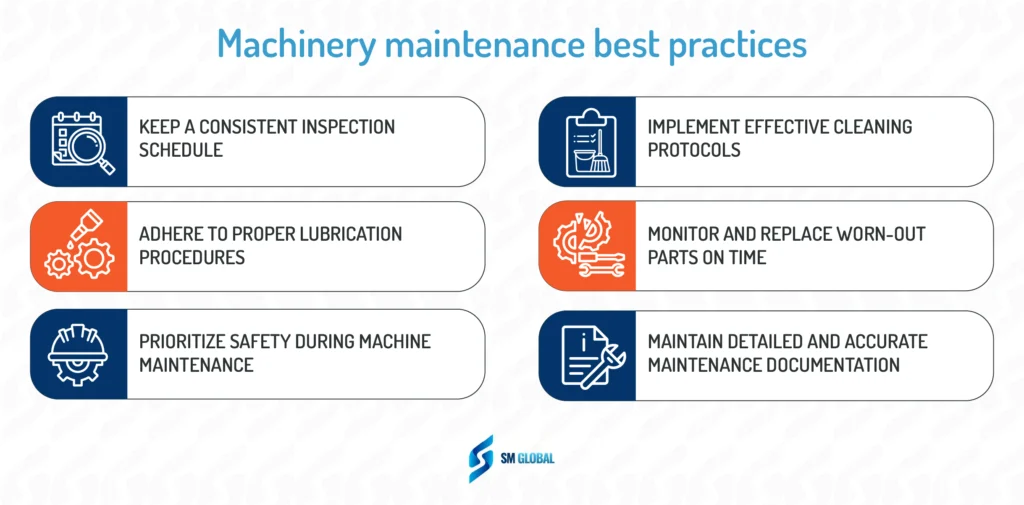
Keep a consistent inspection schedule
A well-structured inspection schedule is the cornerstone of effective machinery maintenance. It ensures that each machine gets enough attention from the maintenance team, based on its priority.
If you are using CBM or PdM, your maintenance and inspection schedules will often be triggered by alerts and data coming from condition monitoring sensors.
For those without such privilege, here are a couple of tips on how to set up equipment inspection schedules:
- Calendarize routine inspections: Plan and schedule regular inspections by using historical data and manufacturer’s guidelines to set intervals and scope. Consider machine usage and age to set the right frequency.
- Develop a comprehensive inspection checklist: Include specific items to examine, performance metrics to measure, and potential issues to watch out for. This checklist should be a living document, constantly refined to meet the evolving needs of the equipment and operational goals.
Implement effective cleaning protocols
Clean machinery not only ensures optimal performance but also prolongs equipment lifespan and promotes workplace safety.
Here are practical steps to institute robust cleaning protocols:
- Identify the cleaning needs of different machines — and schedule regular cleaning sessions based on these needs.
- Choose cleaning solutions that are safe and effective for each machine type. Avoid harsh chemicals that can damage equipment materials or pose health risks.
- Pay extra attention to sensitive parts prone to dirt accumulation or corrosion. Implement detailed cleaning procedures for these critical components to ensure they are thoroughly cleaned without causing damage.
- Be it maintenance technicians, machine operators, or janitorial personnel, people cleaning the machines should have the right tools, know what to do, and how to do it safely.
For an A+, try to keep detailed records of each cleaning session, including areas cleaned, agents used, and any identified issues. This will help you regularly review and optimize cleaning protocols.
Adhere to proper lubrication procedures
Lubrication is pivotal in reducing friction, wear, and tear. Here’s how to optimize lubrication procedures:
- Select lubricants based on the specific requirements of each machine. Consider factors like operating temperature, load, and environmental conditions.
- Store lubricants in a cool, dry place to preserve their effectiveness. Follow storage instructions on the labels to avoid contamination or degradation.
- Adhere to recommended intervals for re-lubrication. Ensure the correct amount and method of application to avoid over or under-lubrication.
- Monitor the condition of lubricants and the performance of the machinery. Modify lubrication practices and schedules in response to observed changes or identified issues.
Monitor and replace worn-out parts on time
Regular monitoring and timely replacement of worn-out parts are an integral part of machine maintenance. Here’s how to do it right:
- Identify parts that are most susceptible to wear and make sure they are regularly inspected. Visual checks and monitoring tools can both do the job, based on the type of part/equipment in question.
- When needed, utilize precision measuring tools to gauge wear levels.
- Identify and stock essential parts to minimize downtime during replacements. Having a CMMS or dedicated inventory management software is incredibly useful for tracking stock levels and forecasting future needs.
- Try to follow the manufacturer’s instructions for replacing worn-out parts. Make sure technicians are properly trained and have access to those instructions.
Prioritize safety during machine maintenance
Maintaining machinery always comes with a certain safety risk. To minimize the chance of an accident or an injury, anyone who performs maintenance work should be aware of — and adhere to — established protocol and safety practices.
Mandatory use of appropriate PPE, detailed and easily accessible LOTO and other safety checklists, as well as proper training, are all integral to equip maintenance personnel with the tools and information they need to perform machinery maintenance safely and effectively.
If you struggle with frequent safety incident reports, consider implementing toolbox talks. These are short meetings (max 15-20 minutes) that concentrate on one specific safety issue or protocol and often include a practical demonstration.
Maintain detailed and accurate maintenance documentation
Nobody likes paperwork – but that doesn’t make it any less useful.
Knowing when a certain maintenance action was performed, by whom, how long the task took to complete, which spare parts were used during the process, etc., represents important historical information that can be used to improve various aspects of machine maintenance.
The easiest way to track all of that info is through a CMMS. By going digital, your teams can automate and optimize the recording of maintenance activities, ensuring accuracy, consistency, and easy retrieval of data.
Armed with that data, maintenance managers can identify recurrent issues, assess the effectiveness of maintenance interventions, and strategize on preventative measures.
Streamline machinery maintenance with FastMaint CMMS
FastMaint CMMS offers a comprehensive solution that encapsulates every facet of machinery maintenance.
FastMaint is designed to simplify and optimize maintenance management, offering features that streamline scheduling, documentation, and analysis. Every maintenance activity is logged, offering a repository of historical maintenance data with actionable reports.
We worked very hard to build an intuitive interface that is simple to use, yet flexible enough to be adapted to the industry you operate in or the type of equipment and maintenance strategies you plan to run.
Start a free trial and use FastMaint CMMS as a reliable ally in your quest to optimize machine maintenance.
Essential Maintenance Metrics Every Planner Needs to Know
Get Free Guide