Essential Maintenance Metrics Every Planner Needs to Know
Get Free Guide
Why Audit Your Maintenance Management Program?
Did you do an audit of all your maintenance activities for the last year?
Don’t look at me like that. I know it sounds rather tedious! 🙁
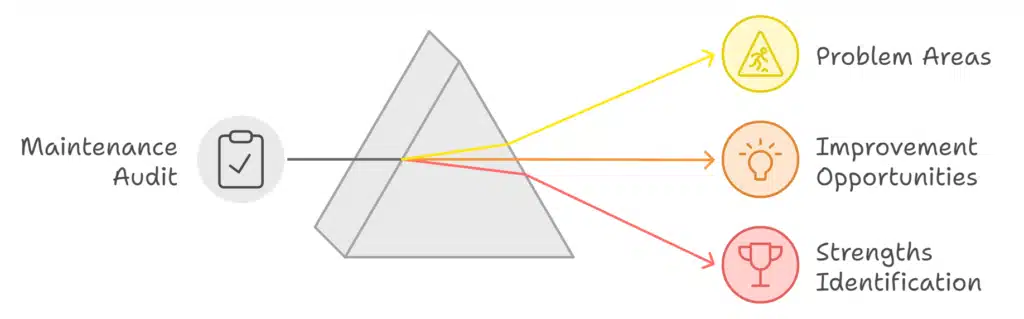
However, it has several benefits. It can help you identify problem areas and scope for improvement. In addition find where you are doing really well in your maintenance management program!
Maintenance operations will change over time. To clarify equipment is added or retired, maintenance personnel change, suppliers change, operations change and so on. With this, new inefficiencies may be introduced or new opportunities for improvements may appear. We can find these sort of things with a periodic audit of the maintenance program.
What To Do In The Maintenance Management Program Audit?
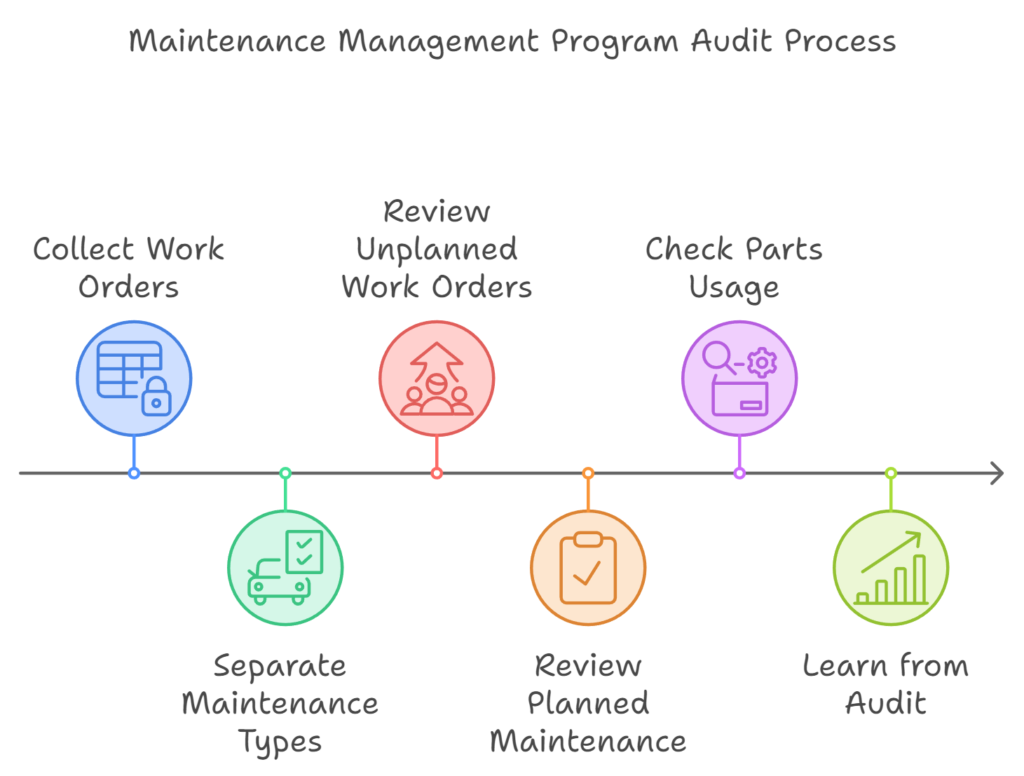
1. Collect information on all the work orders done last year
If you have maintenance management software this will not be hard to do. The software should be able to give you a variety of analysis reports for specific periods. You may be able to do an export of all relevant work orders to do more analysis with other tools. For example with FastMaint CMMS software export data to a comma delimited file. Then open it with spreadsheet software such as Microsoft Excel and do more complex analysis & charting.
2. Separate unplanned maintenance from planned/ preventative maintenance
Group all the maintenance work that was done into two buckets or categories. The categories are a) unplanned or breakdown maintenance and b) planned or preventative maintenance. You will analyze these are two different types of data separately.
3. Review unplanned work orders for problems
Under unplanned work orders look for equipment that seems to be failing frequently or require a lot of unplanned maintenance. This may be a sign that the equipment needs replacement. Or maintenance is not being done correctly. Do problems seem to occur more frequently after certain maintenance team members do the maintenance?
This may be a sign of improperly done maintenance work. They may be skipping work steps! Or do not have the training or experience to identify potential issues that will cause future problems.
Work orders flagged as problem work orders is another clue. They may be taking too much time to complete. Or maintenance technicians are finding additional problems causing completion delays.
Yet another cause could be bad spare parts. Suppliers may be sending poor quality parts that fail early. This will result in a lot of unplanned maintenance!
4. Review planned/ preventative maintenance work orders for problems
Under planned (preventative maintenance) work orders find equipment that seems to be take the most time and money. You may be able to replace equipment with newer equipment that needs less preventive maintenance. Get an idea of how much such equipment is costing you to maintain. See if cheaper alternatives are available. Besides this check and see if some of the preventive maintenance is overkill. See if you are doing more than needed by reviewing manufacturer’s recommendations.
5. Check you maintenance parts usage
Your maintenance software should be able to give you reports of parts you have used over the year. See if you can identify possible bad batches of parts or suppliers who provide poor quality parts. If you identify bad parts you can identify equipment that may need early maintenance because maintenance was done with bad parts from a bad batch. You can also drop suppliers that tend to sell poor quality parts.
Spare part costs are a very big part of most maintenance budgets! Better parts management can help save a lot of money. In addition time since you will have less breakdowns because of bad parts.
What You Should Learn From The Audit
At the end of your audit you should have a good idea of potential problem areas, where you can improve and where you are doing well. This kind of information becomes more valuable as you keep repeating these audits. You can see if you are performing better from year to year.

While reviews at shorter periods e.g. quarterly or semi-annual are also useful, a yearly audit can help smooth out performance fluctuations caused by seasonal changes.
Examples of seasonal changes are equipment running at maximum load to satisfy holiday demand or HVAC issues at the start of winter or summer. These can cause maintenance spikes that can make it hard to compare performance against a prior quarter.
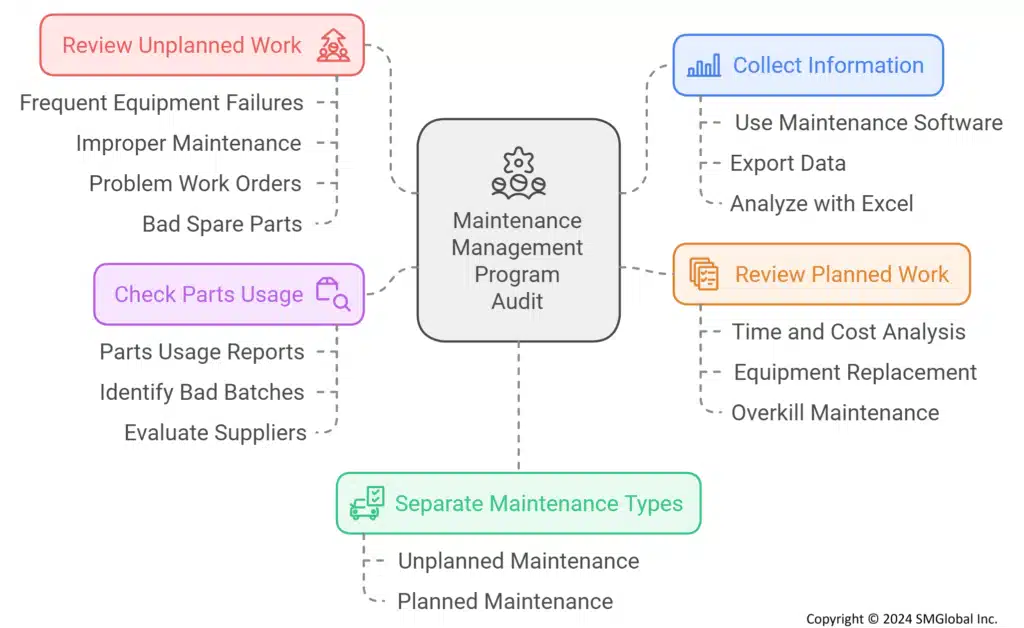
Good Maintenance Management Software Is Essential!
Ultimately to produce useful results you need to be able to collect a lot of data for analysis. This is where good CMMS/ maintenance management software can help. Make sure you have CMMS software that is able to collect and give you back all this data.
Do you need a CMMS/ maintenance software program? Try an online demo or download a 30-day trial of FastMaint CMMS.
Free FastMaint CMMS TrialEssential Maintenance Metrics Every Planner Needs to Know
Get Free Guide