Essential Maintenance Metrics Every Planner Needs to Know
Get Free Guide
Importance Of Equipment Preventive Maintenance
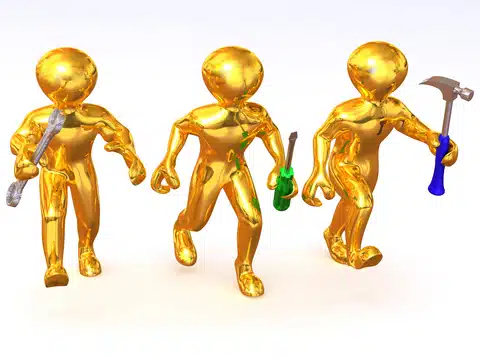
Preventive maintenance is a critical function of a maintenance department. The equipment and machines used for production are a manufacturing or industrial operation’s lifeblood. Equipment breakdowns due to missed maintenance means products not being made or delivered to customers.
Unfortunately maintenance departments are often overworked. When there are other emergencies, preventive maintenance work is the first thing to be dropped.
Have you ever had this happen to you?
Don’t feel too bad if you have experienced this!
I have had more than one customer tell me of how they have dropped needed preventive maintenance due to ongoing maintenance emergencies. My recommendations have often been ways to get emergency maintenance under control and simple baby steps for a preventive maintenance plan.
It is critical to keep such equipment up and running as long as possible. Waiting until a piece of equipment shows signs of trouble can seriously impact production. This in turn, impacts your bottom line.
To combat this, you should use a process called planned preventive maintenance. It is also known as “PPM” or “planned preventative maintenance”.
What does PPM aka planned preventive maintenance entail?
In a nutshell, it means that instead of waiting for the machine to malfunction or stop working completely, you schedule maintenance and inspections at pre-determined intervals. This allows you to discover things that may become issues before they actually become an issue.
A more advanced PPM process would be to add in proactive maintenance where you actively look for sources of failure and fix them in advance.
PPM has been a proven maintenance strategy for a long time. Here we will explain how it works, why it works and how to select the right tools to make it work.
How Planned Preventive Maintenance Works
Each machine has a maintenance plan! This will be based on the manufacturer’s suggested maintenance schedule. It is similar to a car maintenance plan. For example, many car manufacturers recommend you change a car’s oil every 3,000 miles or 3 months, whichever comes first. The transmission should be checked annually. A general tune-up should be done once a year and so on.
You can apply this same idea to machinery and equipment in your organization. Say your conveyor system’s belts should be checked monthly, the gears weekly and the whole system every six months. You set up each of these inspections in the preventive maintenance plan for the conveyor belt. For instance, you can schedule preventive maintenance on an equipment by dates, meter readings, alarm conditions or other maintenance completed.
Fig 1. Schedule preventive maintenance every month (from FastMaint CMMS)
This not only applies to industrial equipment. You can also apply this to office equipment such as computers and copiers. For example, you can include software updates, network tests and toner changes and plate inspections on the preventive maintenance plan for office equipment. You can learn more about different maintenance scheduling options from “How To Schedule Preventive Maintenance Work Orders“.
Why This Maintenance Strategy Works
A reactive approach to equipment maintenance means waiting for something to break before you fix it. So you are not really in control. You will be scrambling to fix problems as they occur. Planned preventive maintenance allows you to take a more proactive strategy.
If you check your equipment on a regular basis, you are more likely to catch small things and repair them before they become larger issues later. Preventive maintenance lowers the chances of losing productivity due to equipment malfunctions or breakdowns. Plus the longer you can keep your equipment running properly, the more productive your business can be.
Other benefits to this strategy include:
- Setting up orders for replacement parts well in advance of when you will need them.
- You can schedule inspections for down times and lessen the impact on production time.
- If you have several pieces of the same equipment, you can often get a volume discount for ordering parts & supplies in bulk or reduce shipping costs
How To Make Preventive Maintenance Planning Easier
If you only have a few pieces of equipment to maintain, a simple spreadsheet may be enough to keep your maintenance schedule on track. But if you have a lot of equipment, or just feel more comfortable with a software package, there are several you can choose from.
A good preventive maintenance software package provides multiple benefits. For example see the benefits for manufacturing plants in “Using Preventive Maintenance Software For Manufacturing“.
What to look for in a maintenance management software program
1. A single interface for all maintenance
Pick a program that can handle both unplanned (breakdown) as well as planned preventive maintenance. This is really important! It makes it much easier to track and manage all the maintenance done on an equipment.
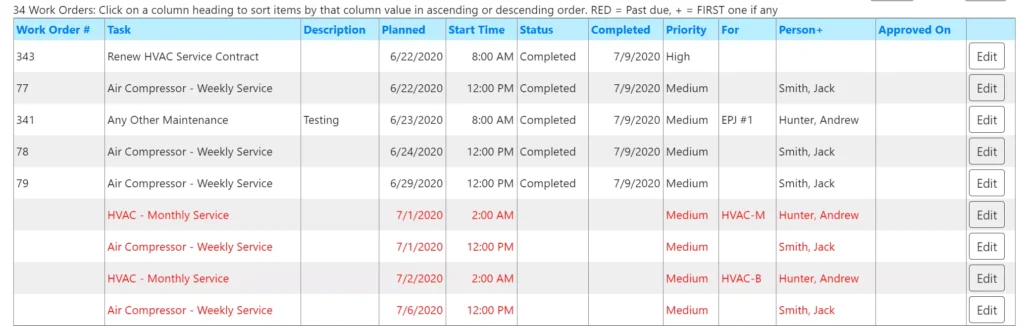
Fig 2. Manage preventive & breakdown maintenance work orders (from FastMaint CMMS)
2. You get maintenance due warnings or alerts
There isn’t much point of using software if it is not going to remind you when each piece of equipment needs to be inspected. That was probably a big reason you choose to use software to begin with. The software should alert you when your equipment is in need of an inspection. It should nag you to death if you miss that deadline! The nags might be annoying. But they help keep you on track with your maintenance plan.
3. Offers a variety of scheduling options
Select software that allows you to choose the method to use when inspections and maintenance should take place. For instance, one piece of equipment might need routine maintenance after a set number of usage hours, another after a set number of months, and even others, a different measure of use. For example industrial plant maintenance software will allow you to schedule maintenance work after a batch of “X” items are processed. The software should allow you to set these for each type of maintenance task on a piece of equipment. This will enable you to customize the maintenance plan to suit your particular needs.
4. Has maintenance inventory management
Solid spare parts & supplies management is one of the most significant source of savings when using maintenance management software. You should be able to track inventory use and get warnings when to re-order parts. After all you cannot do preventive maintenance when the spares & supplies needed are not available!
5. Do not neglect proper maintenance program setup
It is important to setup the preventive maintenance software data correctly. For instance the right equipment information is loaded, the PM tasks are properly scheduled and you have entered maintenance inventory correctly. When you have a lot of assets to maintain it can become hard to start! Start small with the most important items and then add more items with time. See “Eight CMMS/ Maintenance Software Setup Tips” for setup tips and advice.
Goals & Tracking Preventive Maintenance Plans
Good preventive maintenance can help your manufacturing operations run more efficiently. The more up-time you enjoy – the more you can produce. That equates to more sales and a fatter bottom line. The benefits well outweigh the extra work setting up such a schedule will create. It can take some time to set up an effective preventive maintenance plan. But it is worth the initial outlay for software and time to set up. Over time the process will pay for itself. See “7 Tips To Plan Equipment Preventive Maintenance” for some useful tips.
Check plan health & use maintenance calendars
Make sure not to go overboard and run into preventive maintenance problems! A good way to ensure that you are on track is to check your preventive maintenance plan health regularly.
One of the best ways to avoid these problems is to create an equipment maintenance calendar that includes preventive maintenance schedules. Note that you still have to consider breakdown or corrective maintenance (see 7 Breakdown Maintenance Planning Tips) that could happen at the same time and throw out the best laid plans!
Useful preventive maintenance metrics
You should track maintenance backlog on a regular basis. Your scheduled maintenance work that is incomplete or not done at all is your backlog. It includes preventive maintenance as well as corrective maintenance. To help with this there are three main metrics you can use – work order backlog, work order completion percent and average days to complete work orders. See “3 Quick Maintenance Metrics For Maintenance Planners” for more information.
Audit your PM plan regularly
Finally you should do a deep review of reports from your maintenance software on a regular basis, preferably once a year. This reduces the impact of cyclical changes for instance seasonal demands. Your maintenance operations will change over time as equipment is retired, vendors change and employees move on. So doing a regular audit as explained in “5 Step Maintenance Management Program Audit” becomes very important.
Impact of maintenance software
In conclusion many of these steps become a lot easier with a maintenance management program. You will find it easier to start with planned preventive maintenance and keep on track by using maintenance software.
As one of our customers told me “FastMaint (our maintenance software) helped our maintenance staff stay on task daily and make sure all the ‘big tasks’ were being scheduled and getting done. It took a lot of the remembering off of the maintenance team and the maintenance manager. We used to put out fires as a maintenance team, now we can catch them before they start“.
How To Find The Right Maintenance Software?
Need help selecting the right preventive maintenance software for your company, and not sure where to start? Get this free guide to help you identify the right CMMS product for your organization. There are hundreds of programs available, each targeted at different needs. It can become quite tedious finding the right one!
Use the guide to make your selection process a lot faster and easier.
Free CMMS Software Selection GuideEssential Maintenance Metrics Every Planner Needs to Know
Get Free Guide