Essential Maintenance Metrics Every Planner Needs to Know
Get Free Guide
How important is the maintenance department in a manufacturing plant?
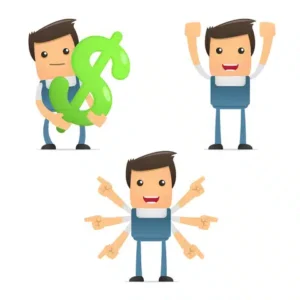
There are many benefits of preventive maintenance software for manufacturing plants. However, in quite a few manufacturing companies higher management tends to see maintenance as a necessary evil! A cost center that adds little value. They may even see the maintenance team not as a crucial part of the company (sometimes maybe a few steps above the janitorial staff!).
This thinking usually results in bad decisions being made for the maintenance team. So often preventive maintenance software for the manufacturing facility gets selected on how nice it looks. For example it has beautiful and extensive reports! Or how well it integrates with other software (ERP, financial and so on). Functionality that will help the maintenance team may not be high on the list.
We have even spoken to maintenance managers who have told us they have had to threaten to quit before they could purchase our FastMaint CMMS software!
This may sound unbelievable. However, it is a sad fact that in many manufacturing organizations the maintenance team gets little respect. Here we will list some benefits that CMMS software can offer a manufacturing plant. This may make it easier to get the approvals you need to purchase the right product for your organization.
Manufacturing Problems That Maintenance Software Can Help Reduce
1. Unable to deliver product because of machine breakdowns
This can be an extremely expensive problem that CMMS software can help reduce. We may have a wide variety of equipment. Each of which performs a crucial step in the manufacturing process. A breakdown of any of them will create a logjam. No more product can be made or delivered to customers.
Each machine will have its own maintenance cycle. Some cycles will be based on time, others on quantity of product made and so on. CMMS software helps maintenance managers create preventive maintenance (PM) tasks and work orders based on these frequencies. For example we can schedule maintenance tasks by a date, day of the week, month, based on another task, based on a meter reading, an alarm an so on.
Fig 1. Work order frequency setting (from FastMaint CMMS)
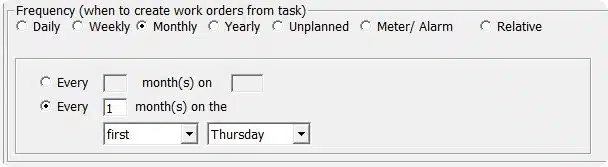
Many CMMS software programs also enable keeping track of maintenance inventory (spare parts & supplies). Not being able to bring a machine back into service because we do not have the spare parts on hand can cause significant product losses.
2. Unable to deliver quality desired because of machines not working to specifications
This is a much more insidious problem. If product quality control is not rigorous, it may not be caught early on. Customers will get poor quality products. Dissatisfied customers then cancel orders resulting in losses to companies. This can be fatal if the company is selling to just a few big customers. Losing them may force the company into bankruptcy.
Again proper maintenance of machinery especially preventive maintenance helps ensure that equipment is running as per specifications. We can find problem equipment due for replacement from CMMS software reports of maintenance work done.
3. Machines requiring early replacement because of poor maintenance
This results in large costs over the long term. If the maintenance team is able to maintain and keep equipment up to specifications they often will not need to be replaced early.
In many industries replacing machinery is a big capital expense. CMMS software can help keep track of maintenance requirements on different equipment so that they do not get forgotten and are done correctly.
Fig 2. Review maintenance work done on an equipment (from FastMaint CMMS)
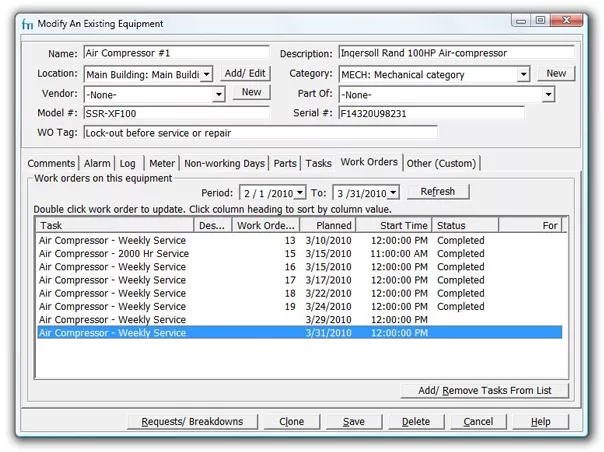
4. Regulatory penalties due to non-compliance
In quite a few industries there are various regulations that companies need to follow during the manufacturing process. Not being able to show or prove that maintenance was properly carried out after certain incidents or when inspections are done, can result in significant financial penalties as well as become a public relations disaster.
Again the record keeping offered by CMMS software can be very helpful in providing a record of work done as well as show that the manufacturer was diligent in maintaining assets and equipment.
5. Inability to manage costs of maintenance & equipment downtime
The maintenance software automatically calculates maintenance statistics. This makes it easier to report to upper management on the status of the maintenance management program. We can get these statistics in a short and easy to understand format (see example below) that we can share.
Better analysis can help maintenance managers find problems with equipment, staffing, spare parts and more. This results in a more effective maintenance management program over time.
Fig 3. Maintenance statistics report (from FastMaint CMMS)
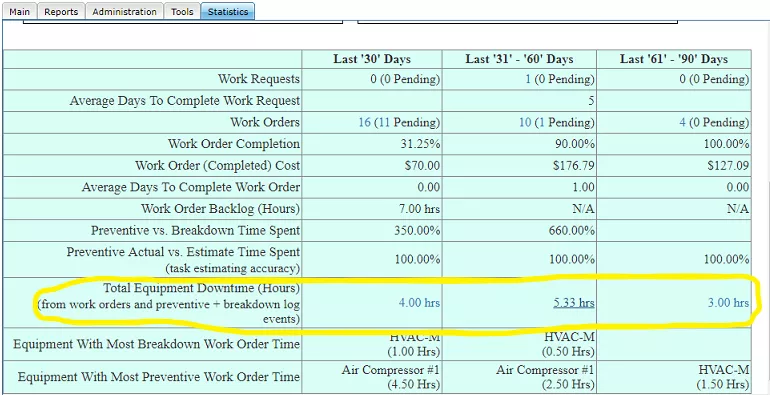
Guide To Select Preventive Maintenance Software For Manufacturing Plants
Since there are hundreds of CMMS software products available it can be quite a challenge finding the right one for your manufacturing plant. To help you identify what you need we have a free CMMS Software Selection Guide that you can download and use.
Free CMMS Software Selection GuideAdditional Reading:
- “Equipment Failure & The Cost Of Failure” from Bin95.com provides a detailed analysis of different costs.
- “Quality Costs” from the Wikipedia attempts to categorize different costs that arise from trying to maintain product quality or lack of it.
- “Equipment Breakdown Insurance” an article on Smart Business Online discusses the benefits of purchasing this insurance and its availability.
- “The value, and cost of quality” from Plant Services Magazine discusses how quality starts to slowly go bad due to bad practices.
Essential Maintenance Metrics Every Planner Needs to Know
Get Free Guide