Bakery Reports Multiple Departments Are Benefiting from Versatile FastMaint Software!
Company Has Been Using FastMaint for Over 13 Years to Boost Efficiency
Facility Supervisor Matthew Sam of Father Sam’s Bakery says the company tried multiple maintenance management programs before settling on FastMaint.
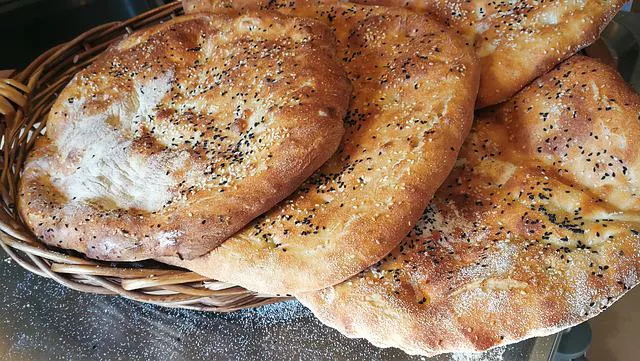
Since making that decision the company has been using FastMaint for over 13 years, including in multiple departments.
“FastMaint is used by our maintenance and sanitation departments,” Sam said. “They run different software editions, but they are all setup very similar. It is great that this software can be utilized in other departments.”
How FastMaint Works:
FastMaint is used by hundreds of customers worldwide to schedule and track all types of maintenance work.
The software includes such features as multiple user accounts, an easy-to-use dashboard, task template creation, fast set-up, work order creation, parts list integration, and much more.
This standalone program is ideal for small and mid-sized companies who want a fast, easy, inexpensive way to manage both planned (preventative) and unplanned (breakdown) maintenance jobs.
Benefits Received by Father Sam’s Bakery:
Sam said his company has received numerous benefits from its use of FastMaint. Three that he stressed in particular were:
Scheduling – Sam said it was especially beneficial to schedule against a calendar and then be able to see if there were any overlaps from the scheduled job tasks. This allows for optimal use of company staff and makes sure essential tasks have the manpower and attention they need to get done on time.
Multiple Users – Another big benefit that Sam indentified was that FastMaint allows multiple users to use the software at the same time. He said this is a big convenience and another important way to optimize everyone’s time.
Organization – Sam particularly likes how use of FastMaint allows his company to stay organized when it comes to the maintenance process. He says the software is great for organizing all aspects of the Maintenance PM process from purchasing to inventory to PM task organization.
The Bottom Line …
Sam’s Bakery began selling bread in July of 1977 and as demand for the bread grew, so did the bakery. What started in a converted garage soon moved to the world-famous Wurlitzer Building in Tonawanda, NY.
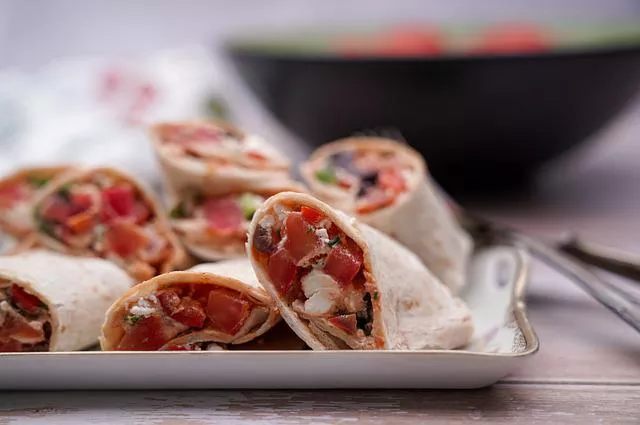
After many years of continued growth in Tonawanda, Father Sam’s built its own state-of-the-art baking facility in Buffalo, NY, moving to the new location in 1996. The bakery has remained there to this day. With that expansion, Father Sam’s also added a complete line of tortillas and wraps.
Today, Father Sam’s Bakery is major food manufacturer that ships throughout the United States of America and Canada. FastMaint has played an important role in the company’s operation for over 13 years now.
Sam says using FastMaint regularly reduces the amount of time required to manage maintenance tasks from 10 hours to 4 hours per week. That is valuable time that can then be used to focus on other important tasks.
For instance, Sam says “I run production also, so I utilize my extra time to lean our manufacturing process.”
Here’s what Sam says About FastMaint:
“FastMaint helps our maintenance staff stay on task daily and make sure all the ‘big tasks’ are being scheduled and getting done. It took a lot of the remembering off of the maintenance team and the maintenance manager. We used to put out fires as a maintenance team, now we can catch them before they start thanks to FastMaint.”