Why use FastMaint CMMS For Maintenance & sanitation scheduling?
Some Customers:
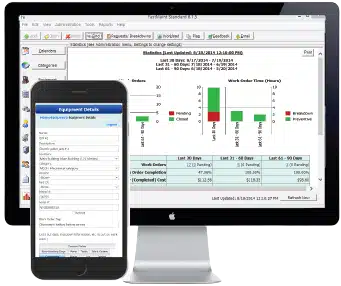
- Easy to use. Import equipment & job instructions from Excel files for fast setup
- Schedule maintenance, cleaning & hygiene jobs by dates, meter readings, alarms and more
- Receive & track maintenance work requests from operators & others
- Keep track of maintenance spare parts, cleaning & disinfection supplies
- Scheduling software used by large & small food manufacturers
- For one-time fee (download on your computers) OR monthly cloud CMMS subscription
Get Free Trial (Download or Cloud CMMS)
Software scheduling & planning features
For maintenance & sanitation departments
Maintenance & sanitation department managers will like the ability to schedule & track equipment maintenance and sanitation activities. Create corrective and preventive maintenance plans. Standardize maintenance & sanitation operating procedures. Better manage food safety compliance requirements. Useful for a variety of food processing companies of all sizes. Track inventory and usage of of maintenance & sanitation supplies to reduce out of stock situations.
Powerful scheduling
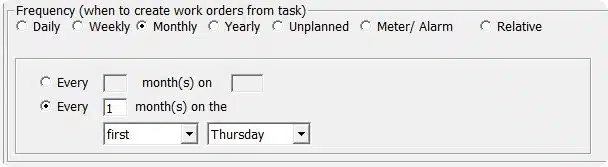
Plan & schedule different jobs with the same simple program interface. Schedule unplanned maintenance due to equipment breakdowns as needed. In addition, schedule maintenance or sanitation procedures on equipment by time (say every Friday) or by meter readings on the equipment (say every 5000 units produced), alarms and so on.
Track jobs with work orders
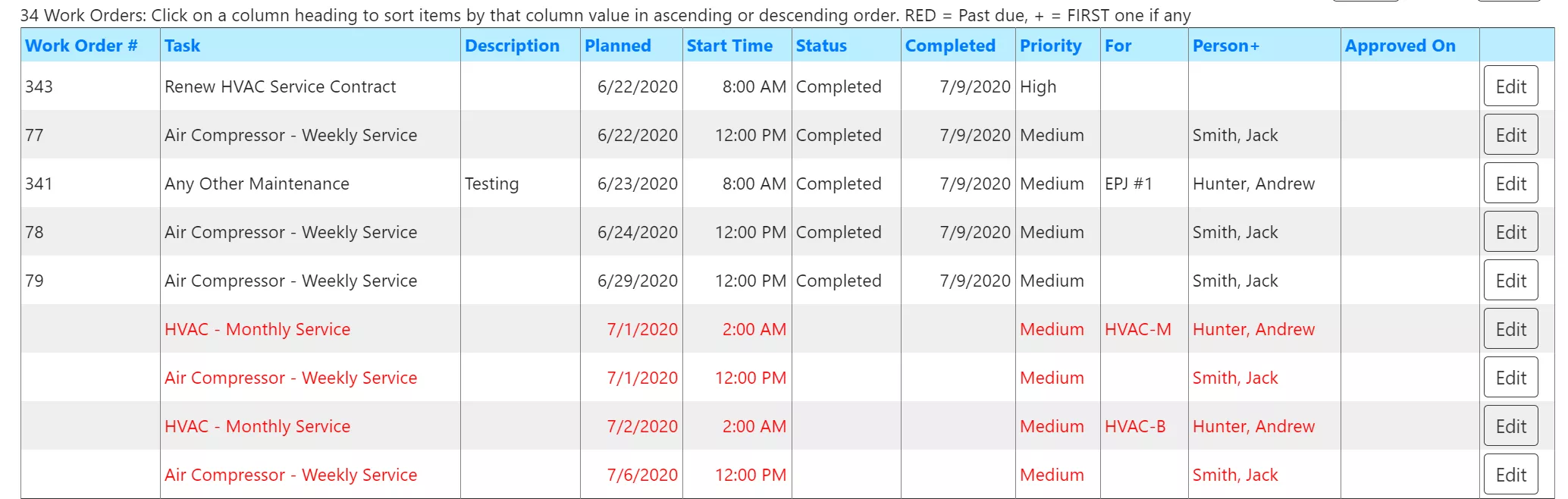
Above all, work orders are used schedule & track maintenance or sanitation procedures to be done by in-house technicians or outside sub-contractors. You can print them out or email them, with reminders sent out when they are overdue. You can also help technicians perform the work correctly by printing pictures and detailed instructions on the work orders. Most importantly this can reduce mistakes that can cause production losses or safety issues.
Excel data import & export
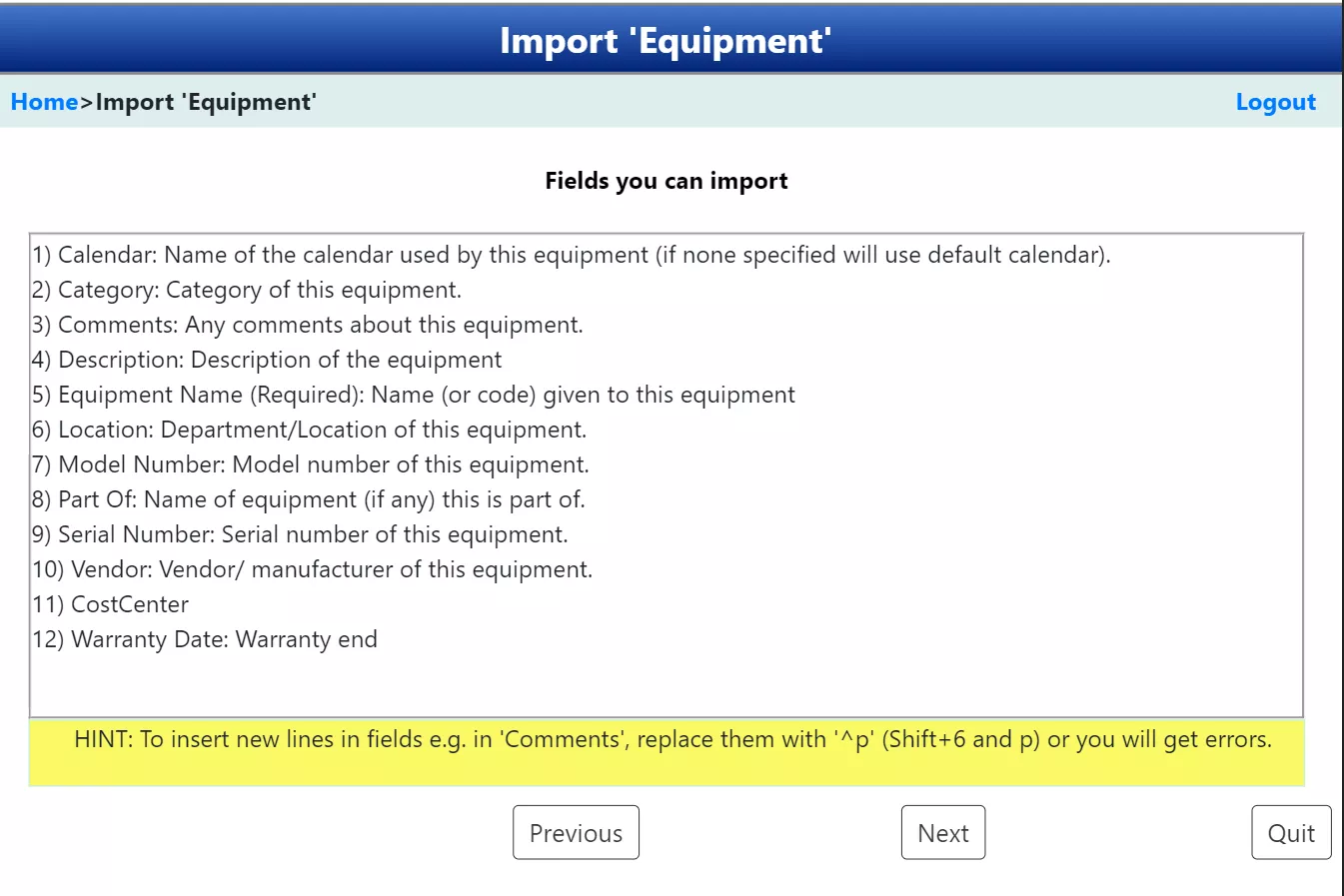
Already have a lot of data in Excel spreadsheets? You can use these files to setup your system and get going. So, you can import equipment, locations, spare parts, job procedures and more.
Use the step-by-step wizard in the Import feature for guidance to map your data to the correct fields.
You can also export data to Excel. For example this week’s work orders, equipment records and so on.
Detailed analytics & reporting
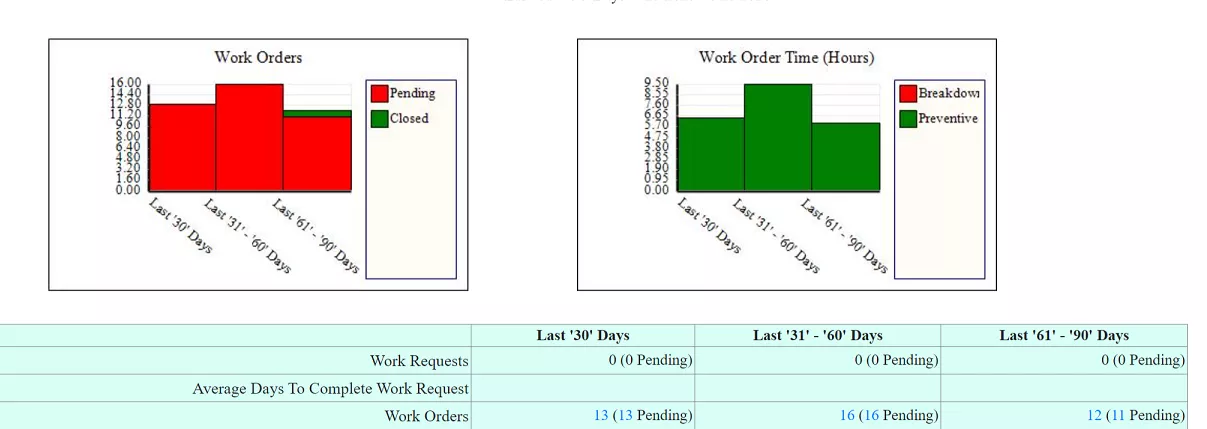
Further FastMaint has a variety of reports that you can print or email. With these reports you can get an idea of work order costs, equipment downtime, spare parts usage and so on. In addition, the one-page Statistics report gives you an idea of your current situation on a single page.
Certainly many reports can be customized! There is an easy to use WYSIWYG Report Editor that will allow you to create your own reports. For instance, you can add logos, insert graphs, add custom fields and so on.
> Compare FastMaint CMMS software editions & features
More about maintenance scheduling from our blog
1. Equipment Maintenance Calendars & Scheduling Preventive Maintenance
When you have several hundred equipment it can be hard to get an idea of preventive maintenance that is due for all the different equipment. We do not want to schedule be too much work in some weeks and too little work during other weeks. This is where reports from your CMMS software (maintenance management software) can be quite helpful. Look for a report like Equipment Maintenance Calendar or Maintenance Calendar.
2. How To Schedule Preventive Maintenance Work Orders
Nearly every equipment or machine needs some kind of regular maintenance. This scheduled maintenance (also called preventive or planned maintenance aka PM) is an often overlooked aspect of maintenance management. This reduces the chance of unexpected failure or repetitive equipment breakdowns. Equipment downtime results in big costs due to lost production, variable product quality and poor customer satisfaction.